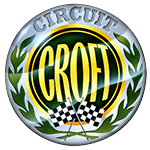
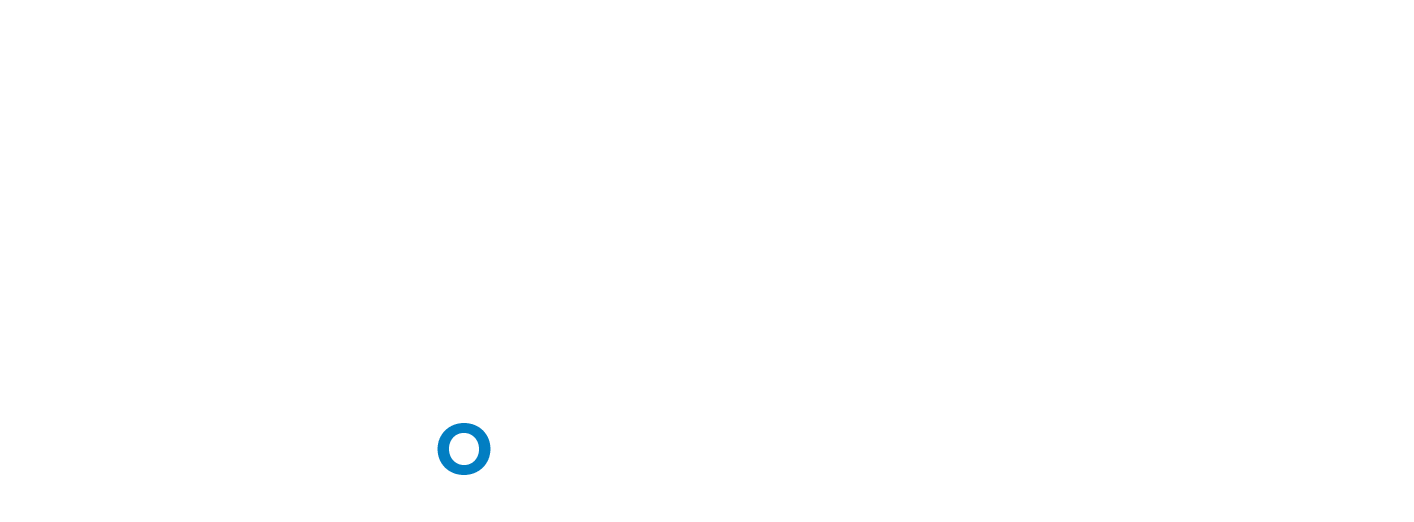
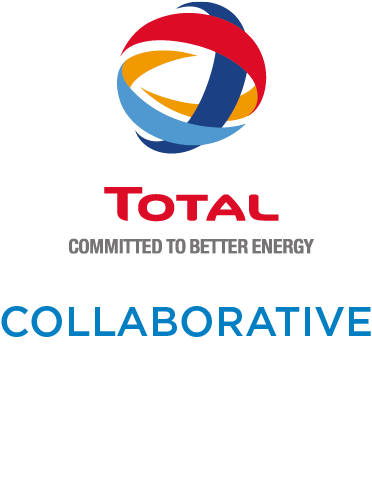
Developed from an RAF airfield to a race track in the mid 1960’s, Croft has a proud racing history and is a permanent fixture on the British Touring Car Championship calendar. The client required works to be completed during a two week closure of the circuit between 25 March and 7 April 2019.

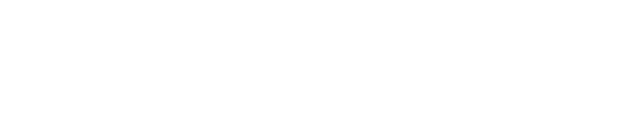
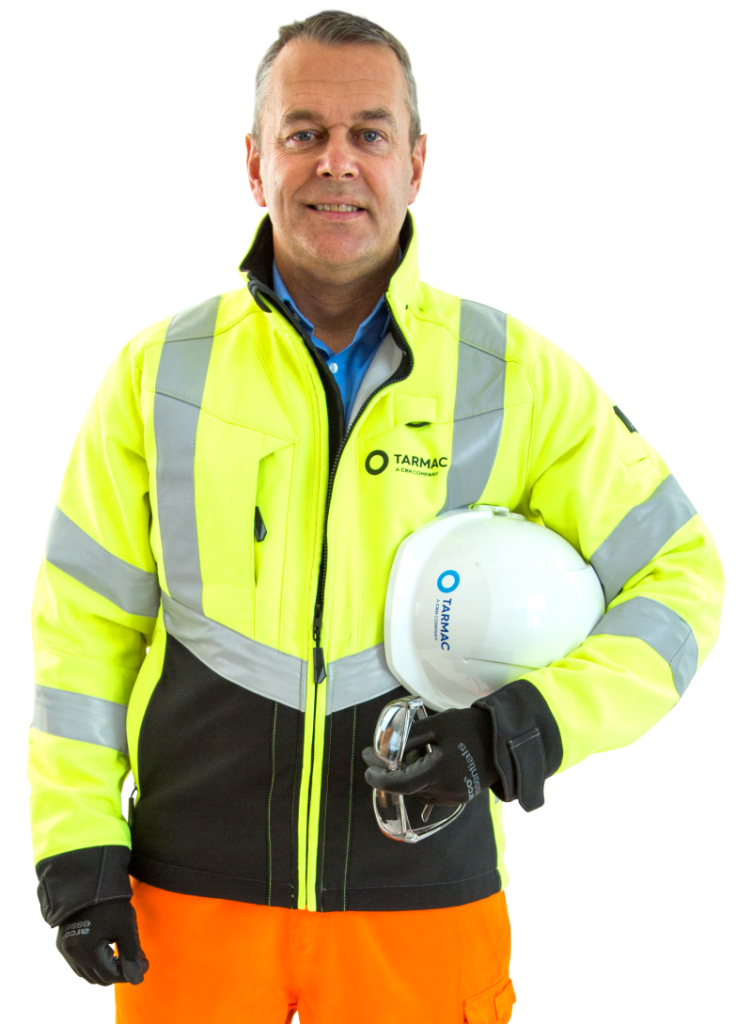

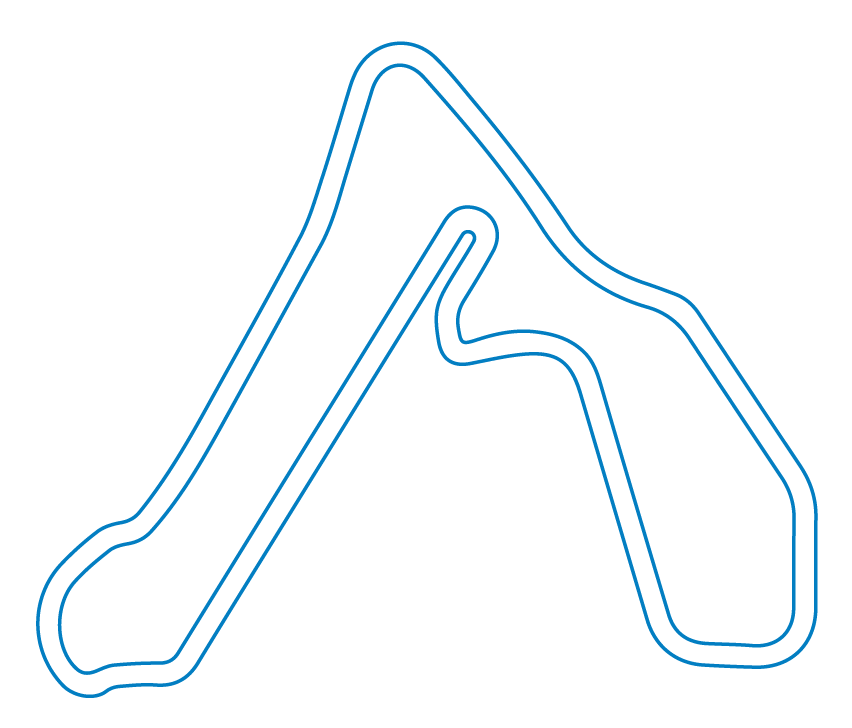

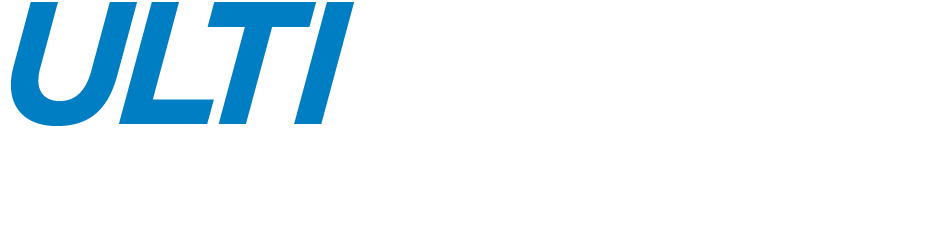
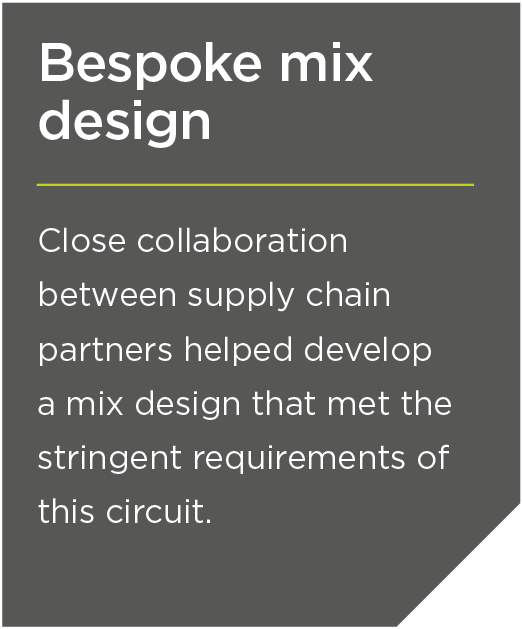
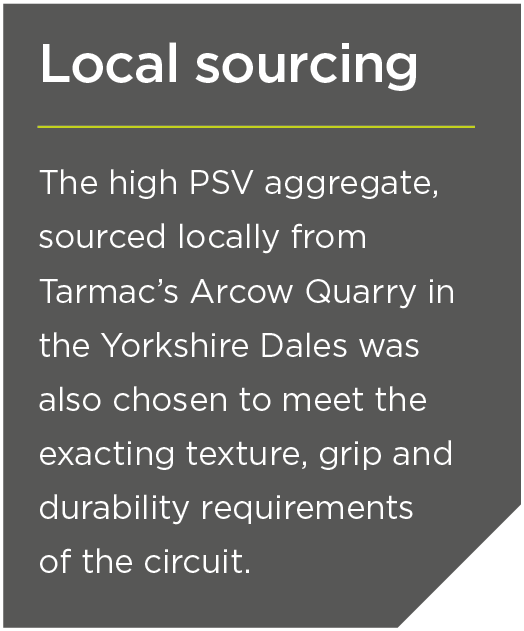
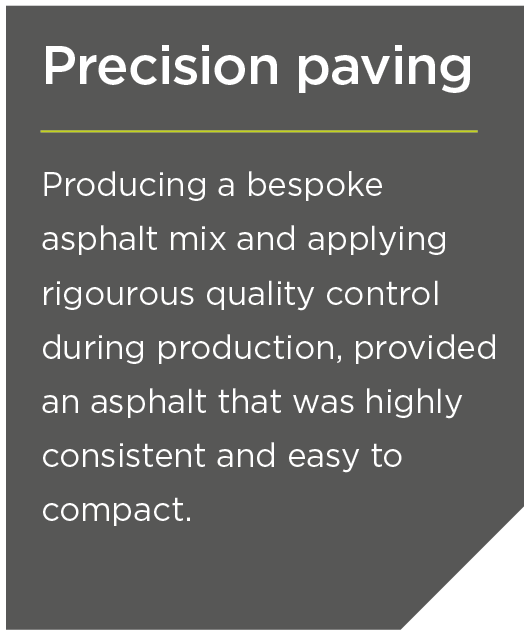
Total Styrelf GP™

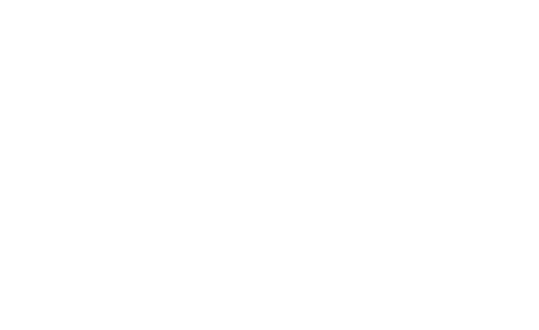
Seamless
surfacing
Automated
paving technology
Non stop
asphalt supply
Planning and logistics
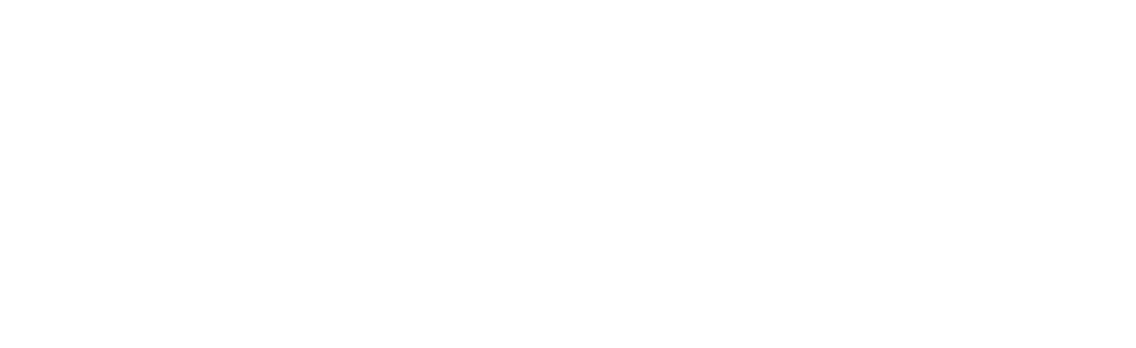
Work was completed on time and on budget over five days in early April 2019. Around 1600 tonnes of asphalt was laid per shift. The client was delighted with the outcome.
Ultimately though, the best judge of the quality of the surface is a professional racing driver.
Here is what Colin Turkington, current and three times British Touring Car Champion had to say about the new surface:
“I was really impressed with the resurfacing at Croft. The new tarmac made a significant improvement to the grip levels in both wet and dry conditions and for a driver, more grip means more speed, so that’s perfect. The big gains I felt were under heavy braking from high speed into Clervaux and Tower bend. Traction from the slow speed corners was also significantly better and in total we were lapping around 2 seconds quicker than last year. That’s a massive gain in lap time!”
“There are endless combinations of settings we can put on the car to achieve the perfect set up and feeling, but ultimately the tyre is your main spring and primary contact patch with the road, so its relationship with the tarmac is crucial. Before the resurfacing, Croft was regarded as a very bumpy track with lots of small undulations making it difficult for the tyre to follow the road, so the setup on the car was always compromise. I found it much easier this time to get the car tuned in for the smooth surface and ultimately we were fast. I wish more tracks were as good as this!”
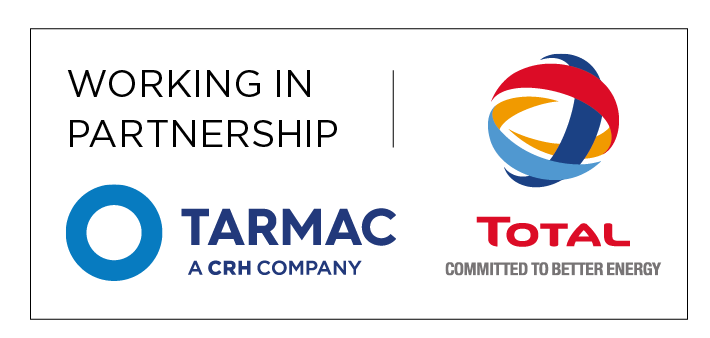
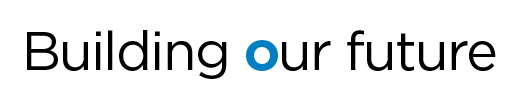